How to Choose the Best Color Masterbatch: 7 Key Criteria for Manufacturers
In today's competitive plastic industry, color is more than just aesthetics—it's a powerful branding tool and a mark of product quality. Whether you're manufacturing household goods, packaging, or automotive components, choosing the right color masterbatch can make or break your product’s appeal.
But with so many options on the market, how do you know which masterbatch is the right one? Let’s explore the 7 most important criteria to help you make an informed and effective choice.
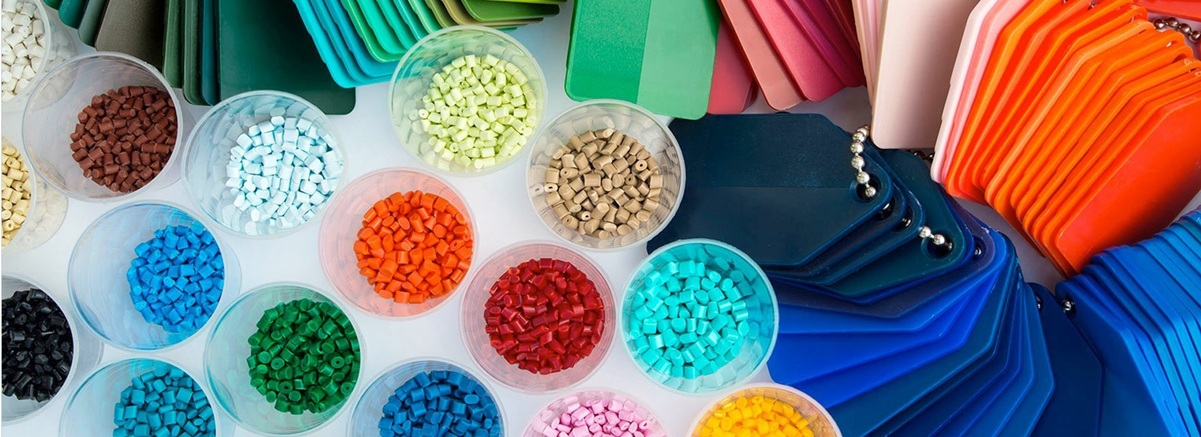
1. Color Accuracy & Consistency
Your brand deserves to shine with uniform color across every batch. A high-quality color masterbatch should deliver:
- Precise color matching based on standard references (e.g. Pantone, RAL)
- Batch-to-batch color consistency
- No visible streaks or uneven tones in finished products
Always request a color sample or plaque before large-scale production.
2. Compatibility with Base Polymers
Color masterbatch must be compatible with the base plastic resin (e.g. PE, PP, PET). Incompatibility can lead to:
- Poor pigment dispersion
- Mechanical property loss
- Processing issues like warping or surface defects
Using the wrong carrier resin can be costly. Make sure your supplier matches the masterbatch to your polymer type.
3. Thermal Stability
Plastics are typically processed at high temperatures (180–300°C). Choose a color masterbatch with:
- Heat-resistant pigments
- Thermal-stable additives
- No color shifting or degradation during extrusion or molding
For high-heat applications, this factor is non-negotiable.
4. UV and Weather Resistance
For outdoor or long-life applications, UV resistance is a must. A good masterbatch should protect against:
- Fading or yellowing from sunlight
- Surface chalking or cracking
- Material brittleness due to prolonged exposure
Ask your supplier about UV-stabilized options for outdoor durability.
5. Regulatory Compliance
Safety and compliance are crucial for sensitive applications like:
- Food packaging
- Toys
- Medical devices
Ensure your masterbatch meets certifications like:
- FDA (USA)
- REACH (EU)
- RoHS
Always request a Certificate of Analysis (COA) or Safety Data Sheet (SDS).
6. Processing Efficiency
A masterbatch should simplify—not complicate—your production. Look for:
- Excellent dispersion
- No clogging or residue
- Easy feeding and dosing
Good flow properties reduce cycle time and improve output.
7. Cost-Effectiveness
While color is critical, so is cost control. Evaluate:
- Pigment strength (allows lower dosing)
- Yield and waste reduction
- Balance between performance and price
Sometimes, a slightly higher-priced masterbatch can lead to big savings in the long run.
Selecting the right color masterbatch isn't just about looks—it's about performance, efficiency, compliance, and cost. By keeping these 7 criteria in mind, manufacturers can ensure superior product quality and customer satisfaction.